Like many successful shops across the country, Ansco Machine is a progressive company. With over 30 years of design and manufacturing experience, they turn a critical eye to the design and functionality of the parts they produce. They actively look for cost savings and efficiencies in both their processes and in their finished products.
Ansco is a full-service contract shop that specializes in milling and turning up to 78” in diameter. They seek out challenging work and one of the many projects they took on was the machining of a cast iron housing that weighs about 750 pounds. The part was too large and cumbersome to be inspected by Ansco’s traditional bridge-type CMM. It was also difficult to check location and relation between features using other conventional methods like dial bore gauges. The older technology was just not sufficient in terms of size, time, or cost.
To take on this very large and challenging job, Ansco sought out the best technology available to ensure their success. They have a long history of looking for ways to improve their processes to expand their business and capabilities, so this was not something unusual for them.
The technology Ansco sought out was the FARO Gage. The Gage is a portable CMM that was designed to enable users to speed through measurement challenges with the most accurate results possible. “The FARO Gage is the perfect solution for this project,” said Wes Suladi, Ansco’s QA Manager. “It is not only the right size to get at all of the features we have to measure, but its accuracy gives me the confidence that what is being reported is true.”
What used to take Ansco over an hour and a half to inspect using conventional technology can now be done in less than twenty minutes using the FARO Gage. That is almost an 80-percent reduction in work time and that equates to a real cost savings in time and productivity.
Ansco’s ability to look past older methods to improve their processes is another example of how progressive and advance-minded manufacturers move to get the best technology that supports their work and their success.
Read the full story
Welcome the 3D Blog, the official blog of FARO Technologies. Check back often for updates from around the world of manufacturing, 3D measurement and technology. FARO develops and markets computer-aided measurement and imaging devices and software. Technology from FARO permits high-precision 3D measurement, imaging and comparison of parts and compound structures within production and quality assurance processes.
Thursday, January 28, 2010
Tuesday, January 26, 2010
General Dynamics Gets $118M Navy Contract
As posted in a recent story in Mass High Tech, General Dynamics Corp.’s Electric Boat unit has landed $118 million from the U.S. Navy for engineering services on ballistic nuclear missile-equipped submarines, according to the U.S. Department of Defense. Under the deal, an option on a previously won contract, Electric Boat will design a missile compartment on submarines equipped with nuclear missiles. Electric Boat will design the compartments for the replacement to U.S. Navy Ohio-class submarines and a new submarine for the U.K. Royal Navy.
The work is expected to be completed by December 2012, and will have the biggest impact on Connecticut, Rhode Island and Vermont as work will be performed in Groton, Conn.; Newport, R.I.; Quonset, R.I.; and Newport News, Va.
The defense industry had its share of rough times in 2009 like the rest of us, but certainly came out much better than average throughout all the economic downturn last year, receiving more than $380 million in contracts for work on submarines back in October. With general manufacturing slowly rising in this early part of 2010, we anticipate to see more and more contracts like this as the year progresses - a very good sign for suppliers and manufacturers.
Read the full story here.
The work is expected to be completed by December 2012, and will have the biggest impact on Connecticut, Rhode Island and Vermont as work will be performed in Groton, Conn.; Newport, R.I.; Quonset, R.I.; and Newport News, Va.
The defense industry had its share of rough times in 2009 like the rest of us, but certainly came out much better than average throughout all the economic downturn last year, receiving more than $380 million in contracts for work on submarines back in October. With general manufacturing slowly rising in this early part of 2010, we anticipate to see more and more contracts like this as the year progresses - a very good sign for suppliers and manufacturers.
Read the full story here.
Friday, January 22, 2010
Nation’s Largest Public Power Provider Enhances Analysis
For more than seven decades, the Tennessee Valley Authority has improved the quality of life in the Tennessee Valley. As a federal corporation and the nation’s largest public power provider, the TVA touches millions of lives. It generates more electricity than any other public utility in the nation and serves about 8.8 million people.
The TVA’s power system is one of the most reliable and efficient in the nation. It has maintained 99.999 percent transmission reliability. Achieving such remarkable consistency requires precise measurement and maintenance of hydro stations and their hydroelectric turbines and generators.
Over time, the concrete used to build dams and other structures shifts, expands, and contracts. This can cause an entire dam to shift. Main rotational bearing surfaces can become deformed due to these pressures, sometimes to the point of becoming elliptical and potentially seizing up.
These important maintenance measurements were previously done with piano wire, optics, and micrometers. These tools lacked the 3D capabilities needed to properly analyze the distortions of embedded components.
Right from the start, the TVA established a unique problem-solving approach to fulfilling its mission-integrated resource management. As Pulitzer Prize winning author James Agee wrote in 1933, “TVA has put a bold foot through a beehive of problems both practical and ethical.” Each issue faced by the TVA is studied in its broadest context and weighed in relation to the others. The TVA has held fast to this strategy of integrated solutions, even as the issues changed over the years.
The FARO Laser Tracker provided such a solution for the TVA. The Tracker allows them to correct deficiencies that were previously unknown. They use the Tracker to measure component deformation and to determine where and what place machining is needed.
Being able to measure in actual 3D and then display results that are easily referenced to integral level was an important feature for the TVA. The 3D capability greatly enhances the analysis of distortions of embedded components. This allows for a more accurate assessment of actual equipment conditions and helps return that equipment to better condition.
With improved information, they are able to make better decisions on what repairs are needed. The improved maintenance helps reduce costly outages, to both the TVA and to its millions of customers.
The TVA’s power system is one of the most reliable and efficient in the nation. It has maintained 99.999 percent transmission reliability. Achieving such remarkable consistency requires precise measurement and maintenance of hydro stations and their hydroelectric turbines and generators.
Over time, the concrete used to build dams and other structures shifts, expands, and contracts. This can cause an entire dam to shift. Main rotational bearing surfaces can become deformed due to these pressures, sometimes to the point of becoming elliptical and potentially seizing up.
These important maintenance measurements were previously done with piano wire, optics, and micrometers. These tools lacked the 3D capabilities needed to properly analyze the distortions of embedded components.
Right from the start, the TVA established a unique problem-solving approach to fulfilling its mission-integrated resource management. As Pulitzer Prize winning author James Agee wrote in 1933, “TVA has put a bold foot through a beehive of problems both practical and ethical.” Each issue faced by the TVA is studied in its broadest context and weighed in relation to the others. The TVA has held fast to this strategy of integrated solutions, even as the issues changed over the years.
The FARO Laser Tracker provided such a solution for the TVA. The Tracker allows them to correct deficiencies that were previously unknown. They use the Tracker to measure component deformation and to determine where and what place machining is needed.
Being able to measure in actual 3D and then display results that are easily referenced to integral level was an important feature for the TVA. The 3D capability greatly enhances the analysis of distortions of embedded components. This allows for a more accurate assessment of actual equipment conditions and helps return that equipment to better condition.
With improved information, they are able to make better decisions on what repairs are needed. The improved maintenance helps reduce costly outages, to both the TVA and to its millions of customers.
Wednesday, January 20, 2010
3D Scanning in Forensics Part 2
As discussed earlier in our Blog (3D Scanning in Forensics Part1) our next entry deals more with the advantages of using 3D laser scanners compared to other methods of capturing data. 3D laser scanners are able to capture thousands of data points per second. The FARO Laser Scanner Photon, for example, has the capacity of capturing 976,000 points per second which is comprised of 711 million pixels per scan! That’s a lot of data. In forensic science, any data that is missed or overlooked could mislead a crime scene in the wrong direction.
One example of this is footprints. Traditional photography cannot give the precise measurements and description as a 3D rendered point cloud. 3D laser scanners have the advantage of capturing the evidence without disturbing the scene. This can be vital in the example of footprints, a decaying body or blood splatter. With the quickness of using laser scanners with the depth of data provided, forensic science will continue to look to 3D laser scanning to correctly investigate crimes.
To read the full article on 3D Scanning Helps Engineers Bore Precise 2.2 mi Tunnel, click HERE.
One example of this is footprints. Traditional photography cannot give the precise measurements and description as a 3D rendered point cloud. 3D laser scanners have the advantage of capturing the evidence without disturbing the scene. This can be vital in the example of footprints, a decaying body or blood splatter. With the quickness of using laser scanners with the depth of data provided, forensic science will continue to look to 3D laser scanning to correctly investigate crimes.
To read the full article on 3D Scanning Helps Engineers Bore Precise 2.2 mi Tunnel, click HERE.
Thursday, January 14, 2010
How Does Quality Control Play into the Automotive Industry's 2010 Future?
As reported in the AP, we are starting to see "signs of increased confidence that the US auto market bottomed out last year and will improve in 2010." There have been reports of many automakers considering hiring new employees as they anticipate a recovery in vehicle demand this year. The anticipated high demand also has manufacturers like GM considering reopening some closed factories.
What does this mean for the manufacturing industry? Well of course an increase in vehicle production means an increased demand for parts and services. Many of the automotive suppliers that faced one of their hardest years to date in 2009 are eagerly anticipating what 2010 will bring. The Detroit Free Press reports, "The start of the Detroit auto show was a day for looking ahead with hope," where "automakers talked about the production they're adding back for hot-selling models" and "General Motors and Ford vowed a blitz of competitive vehicles."
With the increased demand ahead in 2010, Chrysler, now owned by Fiat Group SpA, is not only paying close attention to managing the increased volume carefully but also on the quality of the cars they produce. "The best way to change the public's perception of poor quality is to produce better vehicles," said Sergio Marchionne, the head of Chrysler. With the other US automakers likely following in this same fashion to gain back market share in 2010, we will have to expect the demand on first and second tier automotive suppliers will be greater than ever to produce high quality parts with a very minimal margin of error.
In a year as important as this, it is crucial for everything to go right within the domestic automotive industry. The production must be on point, the pricing affordable yet profitable, the decisions sound, and most importantly the quality in place. This will likely be a "make it or break it" year for the US auto companies, and it would be a shame to see them fail over quality issues. With increasing competition from the foreign markets, especially in the past few years, domestic automakers have a lot to overcome in 2010. Outlooks seem hopeful, though, with most analysts anticipating moderate growth in 2010 with a stronger pickup toward the end of the year.
Read the full story from the AP.
Read more about how to control quality issues.
What does this mean for the manufacturing industry? Well of course an increase in vehicle production means an increased demand for parts and services. Many of the automotive suppliers that faced one of their hardest years to date in 2009 are eagerly anticipating what 2010 will bring. The Detroit Free Press reports, "The start of the Detroit auto show was a day for looking ahead with hope," where "automakers talked about the production they're adding back for hot-selling models" and "General Motors and Ford vowed a blitz of competitive vehicles."
With the increased demand ahead in 2010, Chrysler, now owned by Fiat Group SpA, is not only paying close attention to managing the increased volume carefully but also on the quality of the cars they produce. "The best way to change the public's perception of poor quality is to produce better vehicles," said Sergio Marchionne, the head of Chrysler. With the other US automakers likely following in this same fashion to gain back market share in 2010, we will have to expect the demand on first and second tier automotive suppliers will be greater than ever to produce high quality parts with a very minimal margin of error.
In a year as important as this, it is crucial for everything to go right within the domestic automotive industry. The production must be on point, the pricing affordable yet profitable, the decisions sound, and most importantly the quality in place. This will likely be a "make it or break it" year for the US auto companies, and it would be a shame to see them fail over quality issues. With increasing competition from the foreign markets, especially in the past few years, domestic automakers have a lot to overcome in 2010. Outlooks seem hopeful, though, with most analysts anticipating moderate growth in 2010 with a stronger pickup toward the end of the year.
Read the full story from the AP.
Read more about how to control quality issues.
Thursday, January 7, 2010
FARO CAM2 Software Tips & Tricks | Reference Point System Alignment in CAM2 Q
Reference Point System Alignment in CAM2 Q
The measurement of castings and press parts, where parts are generally free-form and do not have flat surfaces and straight lines commonly used to define coordinate systems, is a challenge faced by several users.
Measuring molds is one solution that is often used to measure this type of part. The molds contain a set of control points that allow quality departments to determine if their parts are within specification. Not only are these molds expensive, but they are also specific to a particular part. More importantly, these molds do not allow quality departments to control points that are not controlled by the mold.
Reference Point System, commonly known as RPS, is a technique that was introduced to overcome this limitation. Using this technique, Quality departments are able to define an alignment for their parts, and consequently are able to use 3D measurement devices to control them.
Let’s walk through the process of performing such an alignment in CAM2 Q:
In the part displayed, the Design department has provided the Quality department with instructions to align the part for measurement using 3 points and 2 circles. The positions of the RPS points are provided in a text file and the circles have been identified visually.
Step 1: The operator loads the CAD part and prepares his nominal features for the RPS alignment.
Step 2: The user measures the 3 points and the 2 circles.
Step 3: The user creates his alignment. He defines the components of each feature that have a weight on the alignment. Here we see that CAM2 Q automatically checks for the points that only the Z direction is interesting.
Step 4: The part is pre-aligned to the measurement device.
Step 5: The user identifies the points that were not initially taken within the home-in zone. He will re measure those points, using the Remeasure command.
Step 6: Since an alignment is active, the software now provides the user with a top view of the point and guidance to the correct location where he must measure the point.
With 6 easy steps, the operator has now accurately aligned his part and can start measuring it.
Learn more about CAM2 Q.
The measurement of castings and press parts, where parts are generally free-form and do not have flat surfaces and straight lines commonly used to define coordinate systems, is a challenge faced by several users.
Measuring molds is one solution that is often used to measure this type of part. The molds contain a set of control points that allow quality departments to determine if their parts are within specification. Not only are these molds expensive, but they are also specific to a particular part. More importantly, these molds do not allow quality departments to control points that are not controlled by the mold.
Reference Point System, commonly known as RPS, is a technique that was introduced to overcome this limitation. Using this technique, Quality departments are able to define an alignment for their parts, and consequently are able to use 3D measurement devices to control them.
Let’s walk through the process of performing such an alignment in CAM2 Q:
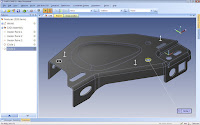
Step 1: The operator loads the CAD part and prepares his nominal features for the RPS alignment.
Step 2: The user measures the 3 points and the 2 circles.
Step 3: The user creates his alignment. He defines the components of each feature that have a weight on the alignment. Here we see that CAM2 Q automatically checks for the points that only the Z direction is interesting.
Step 4: The part is pre-aligned to the measurement device.
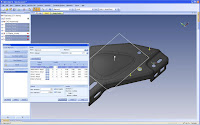
Step 6: Since an alignment is active, the software now provides the user with a top view of the point and guidance to the correct location where he must measure the point.
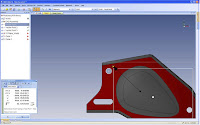
Learn more about CAM2 Q.
Tuesday, January 5, 2010
Precise Measuring in Tunneling
Tunnels have been a part of our civilization since the ancient times. Tunnels were used extensively for irrigation and for pedestrian passages. Engineers in the ancient world constructed tunnels to redirect water during dry seasons and to provide secret access into the temple for royalty. As time went on more elaborate tunnels were made for drainage in the construction of aqueducts during the Roman times. It wasn’t too long that engineers were able to design and excavate tunnels large enough to provide mass transit for railways and eventually automobiles.
As you can imagine, a tunneling project takes a vast amount of time, labor and revenue to complete. In order to maximize the labor without costing additional time and money, engineers with the Vintebro Project used 3D laser scanning throughout the process. Mika AS, a civil engineering company in Oslo Norway, specializes in hard rock excavations with an expertise in tunneling. Mika invested in a FARO Laser Scanner so they could conduct virtual scans of the tunnel to ensure that the aligning was precise. Not only did the laser scanner reflect accuracy within the tunnel walls but it also provided engineers with vast amounts of data in the shortest amount of time.
To read the full article on 3D Scanning Helps Engineers Bore Precise 2.2 mi Tunnel, click HERE.
As you can imagine, a tunneling project takes a vast amount of time, labor and revenue to complete. In order to maximize the labor without costing additional time and money, engineers with the Vintebro Project used 3D laser scanning throughout the process. Mika AS, a civil engineering company in Oslo Norway, specializes in hard rock excavations with an expertise in tunneling. Mika invested in a FARO Laser Scanner so they could conduct virtual scans of the tunnel to ensure that the aligning was precise. Not only did the laser scanner reflect accuracy within the tunnel walls but it also provided engineers with vast amounts of data in the shortest amount of time.
To read the full article on 3D Scanning Helps Engineers Bore Precise 2.2 mi Tunnel, click HERE.
Subscribe to:
Posts (Atom)